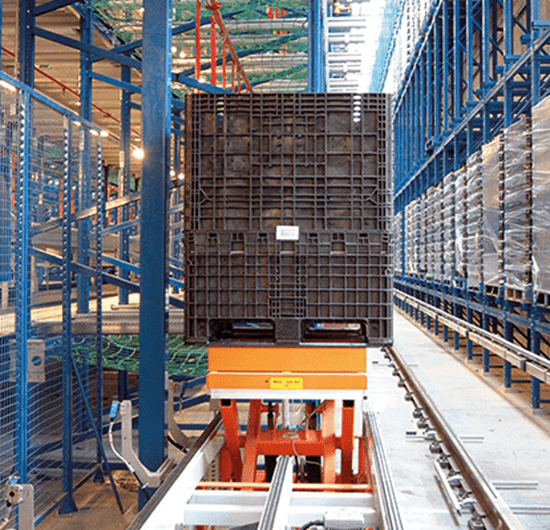
Rozwiązanie podnoszące dla w pełni zautomatyzowanego magazynu
Automatyzacja napędzana precyzyjnymi rozwiązaniami podnoszącymi
Tak pomogliśmy integratorowi systemów sprostać wymaganiom zautomatyzowanego magazynu. Nasze rozwiązanie działało niezawodnie w zintegrowanym systemie dźwigów, przenośników i podnośników.
Dematic projektuje i tworzy inteligentne zautomatyzowane rozwiązania dla produkcji, magazynowania i dystrybucji.